- | 8:00 am
This building’s deconstruction resulted in just two buckets of waste

Two buckets. That’s all that was left at the end of the day when Nexii, a concrete alternative start-up, tore down one of its first demonstration projects. A 700-square-foot showroom and model home displaying Nexii’s building technology was constructed in 2019 near Vancouver to prove the buildability of the new material, which has far lower emissions than conventional concrete. Now, with the project’s teardown, the company is proving that the material can be deconstructed and rebuilt elsewhere, with very little waste heading to a landfill in between.
“Our buildings are designed for rapid assembly,” says Zosia Brown, Nexii’s vice president of sustainability, “and they’re equally able to rapidly disassemble.”
The project is an example of circular design that Nexii, one of Fast Company’s Most Innovative Companies for 2022, is hoping to make more common through its sturdy panel-based construction system.
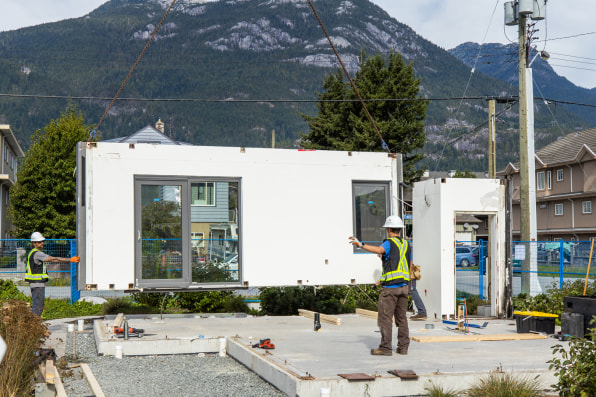
[Photo: courtesy Nexii]
Assembly requires little more than craning the pieces onto a foundation and bolting them together. In 2021, the company’s materials were used to construct a Popeye’s fast food restaurant in just two weeks. They’ve also built projects for Starbucks and are currently working on a project for Marriott hotels. They’re also partnering with companies like Siemens and Honeywell to provide the building materials for net zero industrial facilities.
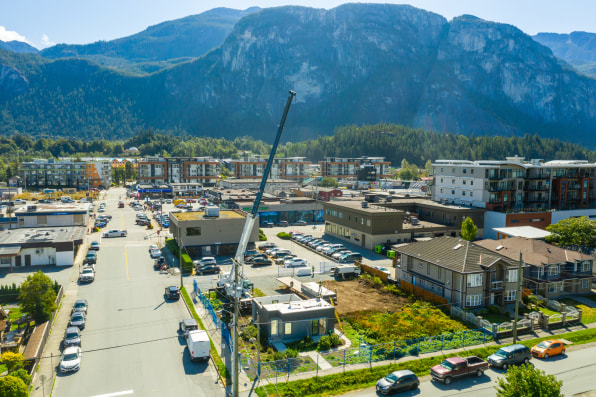
[Photo: courtesy Nexii]
Tested to withstand fires, floods, hurricanes, and earthquakes, Nexii’s building panels are designed to have very long lives and be easily rebuilt again and again. So when the lease ran out on the site of its showroom, the company began looking for a new location and a new owner. They found a buyer, and re-assembly of the building will begin next month. “We had a real interest in walking the talk on the ability to deconstruct and [show] what that looks like,” Brown says.
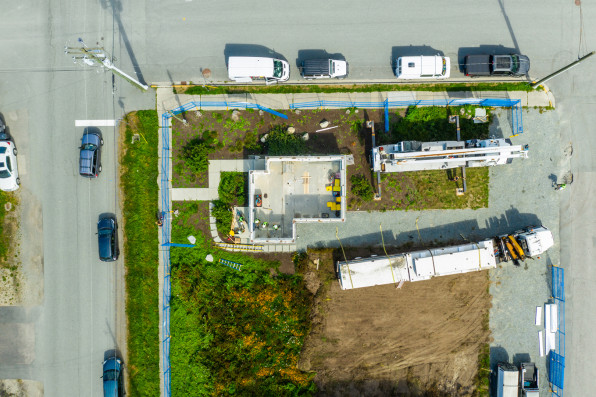
[Photo: courtesy Nexii]
In partnership with the consultancy Light House Sustainability Society, Nexii’s showroom deconstruction was meticulously tracked, and a case study on the process was recently published. Over just six days, the building was taken apart piece by piece, and carefully stacked onto flatbed trucks for transportation to the next building site. Almost every part of the building was saved for reconstruction. “We had 99.8% diversion from landfill at the end of the day, which is huge,” Brown says.
From the building itself, the waste fit inside those two buckets. It consisted of just the sealant used to create an airtight connection between the panels, small sections of weatherproofing, and “a couple of screws that we weren’t able to reuse,” says Brown. “The main waste that was generated was some typical bits and bobs of just having people on site for six days, like coffee cups, lunch waste, and that sort of thing.”
The disassembled building will be reassembled in its original design next month on Saltspring Island, British Columbia, where the new owner will use it as a guest house. It’s an example of what Brown hopes Nexii’s panels can do going forward, which is to use their durability to find new uses far into the future.
“The design life cycles of the conventional buildings that go up are much shorter than the potential lifecycle of the materials and the construction themselves. That leads to a lot of waste,” Brown says. “We want to be a company that’s doing things differently in that regard.”