- | 6:00 am
Nike shoes didn’t just inspire these acoustic panels, they are the panels

Before founding his own studio, Michael DiTullo worked for nearly a decade designing shoes for Nike, Jordan, and Converse. So perhaps it should come as little surprise that when he was hired to design acoustic paneling for Kirei, he crafted it like one giant recycled shoe.
Its name? Air Baffle. And it’s the first time ever that a new recycled Nike material called Fluff will make its way into a commercial product outside the company.
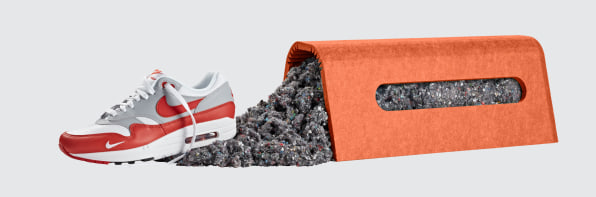
[Photo: courtesy Kirei]
Perhaps this story sounds small. However, acoustic paneling (aka baffle) is a quiet juggernaut in the world of architecture. It represented a $7 billion global market in 2020. It’s basically soft stuff that you put onto walls to absorb sound. Generally built with rounded edges and plastic-derived foams, materials and design work in concert to break up large, loud sound waves into tinier ones. As these sound waves bounce around inside the baffle, they actually bump into one another and cancel each other out.
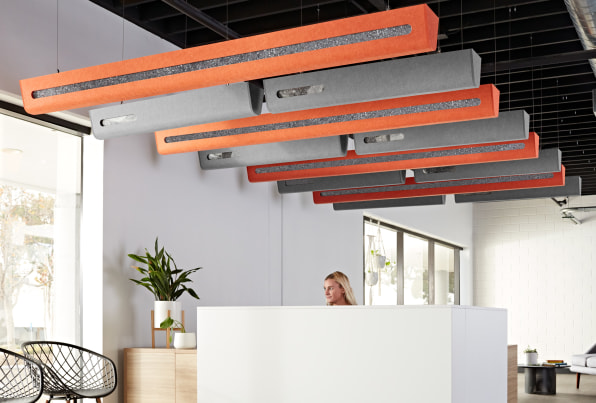
[Photo: courtesy Kirei]
“That’s how you get this idea of sound waves being ‘deadened,’” DiTullo explains. They literally kill one another! (But don’t feel bad about that; acoustic panels are a big reason why you can eat at a restaurant and still hear the person next to you.)
When developing a new baffle for Kirei—a sustainability focused acoustic paneling company—DiTullo was searching for a way to make his design more eco-conscious. It already used a shell made from dozens of recycled plastic water bottles. But he wanted to fill the hollow container with something soft and environmentally friendly to absorb more sound, and perhaps mitigate waste in the process.
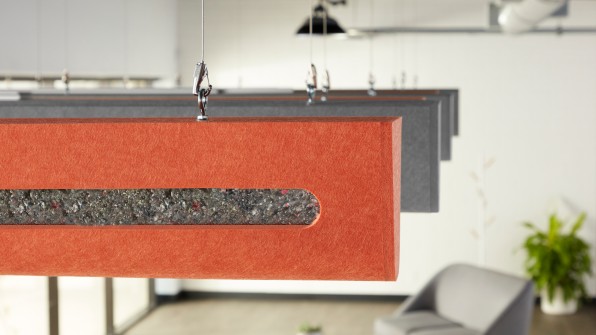
[Photo: courtesy Kirei]
And that’s when his mind returned to his days at Nike. Nike has a program called Nike Grind, in which it collects old sneakers and grinds them up to make new products. The Nike Grind we’ve seen thus far also tends to be a rubbery material, created from ground-up outsoles. This type of Grind has been repurposed for Nike’s own shoes. It’s rarer to see the material celebrated within architecture—Nike Grind used in carpet padding and gym tiles is well and good, but it doesn’t exactly scream “object of desire.”But as it turns out, the Grind program has many materials beyond its famous, rubbery “Grind” that it’s trying to find a second life for, including something called Fluff. Instead of being made from the bottom of the shoe, Fluff is made from the top of the shoe—a shoe’s “upper” that might have leather, canvas, and other soft components.
Ground up, Fluff looks like cosmic dryer lint, with flecks of colors. “You get this consistent inconsistency,” DiTullo says. “It’s so varied, but it’s so constantly varied that it looks uniform.”DiTullo realized that Fluff would work perfectly inside his baffle design. “It’s basically stuffing this thing full of cotton balls,” DiTullo says. But Fluff looked good enough that he didn’t want to hide it. At Nike, he learned that design should highlight the mechanical technologies inside a shoe, and he wanted to do the same with the Fluff inside Air Baffle. So he cut a long oval into the shell with the same shape as an Air Max air bubble. (Because acoustic paneling is often chosen by architects and interior designers years in advance of a building being opened, it may be a while before you actually see Air Baffle in person.)
As DiTullo points out, Nike’s Tinker Hatfield designed the original Air Max in 1987 after being inspired by the Centre Georges Pompidou in Paris—which features an exposed, bubble-like escalator outside of the building.
“It’s ironic we have a shoe, the Air Max One, inspired by a building,” DiTullo says. “And now this building material [Air Baffle] is inspired by a shoe.”